Whether it’s an aerospace prototype project or a new automotive programme, the road to quality begins long before final assembly. Rupert Musgrove, UK Managing Director of G&P, explains why improving quality control higher up the supply chain can lead to lower costs, improved efficiencies, and zero defects on the production line.
WHAT QUALITY COSTS
Most companies understand that stringently monitoring quality in the supply chain is hugely important, but for complex products manufactured in the automotive, aerospace, and off-highway industries, it becomes a necessity. In the automotive industry, for example, around 80 percent of product value is added by external suppliers, with a typical programme directly or indirectly engaging thousands of suppliers across Tiers 1, 2, and 3.
Utilising such a wide-reaching and diverse portfolio of tiered suppliers, whilst certainly adding value, also presents a unique challenge – each supplier generally carries a very small risk of product defectivity, but this rises in correlation with the number of suppliers in the chain. Suddenly, the risk of receiving poor-quality parts becomes very real. Just look at the number of expensive vehicle recalls and quality issues over the past few years – practically every original equipment manufacturer (OEM) in the automotive and aerospace industries has been affected at some point, and it almost always makes headlines.
With the sheer number of suppliers involved, it’s not unusual for quality issues to escape when pushing to get production over the line. However, this almost always has a detrimental impact in the long term, especially from a brand and financial perspective.
This problem can also be amplified by the fact that companies responsible for shipping sub-standard products are not typically those responsible for the eventual warranty costs.
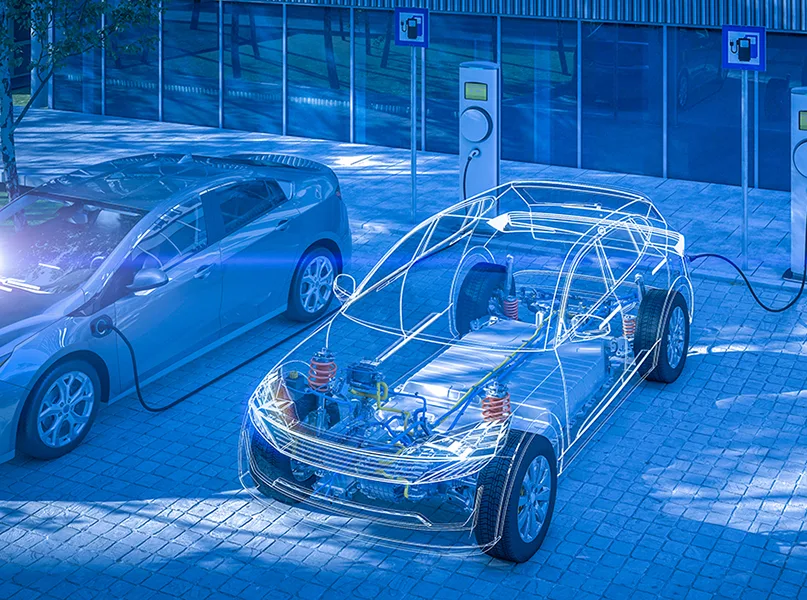
THE COST OF QUALITY
Without effective management, quality-related costs can be as high as 15-20 percent of sales revenue. That is why investing in quality management processes throughout the supply chain is one of the most effective methods to reduce overall costs associated with poor-quality parts.
There are four key areas in which the cost of quality impacts a business: prevention and appraisal costs, which together are the cost of good quality, and internal and external failure costs, which combined are the cost of poor quality.
For example, there may be internal costs associated with rectifying issues, but there can also be external costs and loss of sentiment if a product or project goes to market with demonstrable quality issues or failures. The four costs of quality were first described by American quality expert and businessman Armand V. Feigenbaum in a 1956 Harvard Business Review article but are nevertheless just as relevant today.

Let’s look at each of these in more detail:
Cost of good quality:
- Prevention costs – Proactive investment aimed at avoiding effects and issues. Examples are the introduction and measurement of quality management systems, established specifications, implementing quality plans, and providing training programmes to upskill the team.
- Appraisal costs – These are costs associated with measuring and monitoring activities to meet quality standards, such as the testing of parts, materials, equipment, processes, supplier ratings, and audits.
Cost of poor quality:
- Internal failure costs – The financial costs of quality issues before the product reaches the market, i.e. reworking, reproducing, scrapping, failure analysis, and addressing issues.
- External failure costs – Expenses from issues once the product is in the market – recalls, warranty claims, customer service, and legal liabilities. It also includes the effect these might have on the company’s reputation, value, and future profitability.
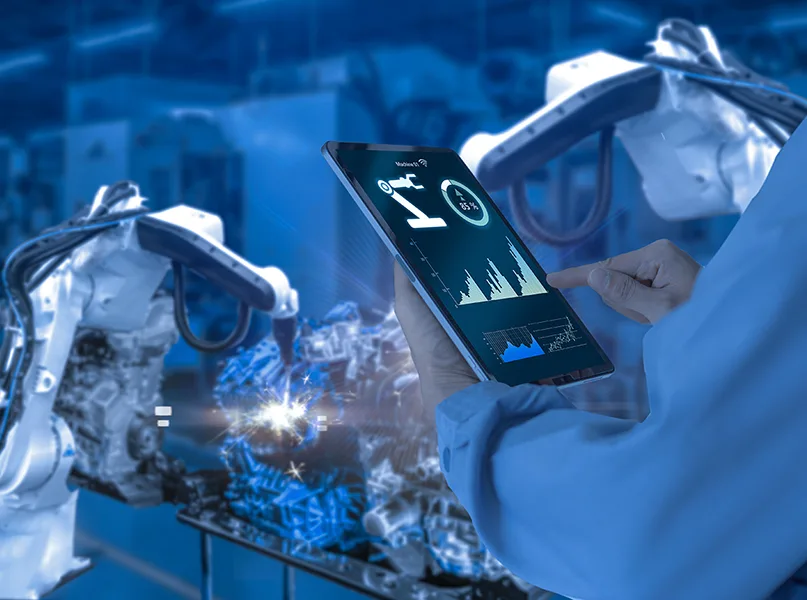
So, what are the most common causes of poor quality in complex product supply chains? The most frequent issues are parts that don’t meet required specifications, manufacturing defects, inadequate process control, assembly errors, and insufficient component information and traceability.
In sectors with complex products, quality issues can be catastrophic. It is not just an immediate financial issue either – there are reputational and legal factors to consider. As long as an OEM does not have full and effective management of its entire supply chain, the quality of its final product will always carry risk.
The only true solution? Robust quality management – and not just at the final assembly stage.
SPECIALIST QUALITY MANAGEMENT SOLUTIONS
For companies seeking to better understand where quality issues may be arising in their supply chain, G&P brings its wide-ranging expertise to bear. The multi-award-winning company provides a holistic approach to quality management backed by 30 years of international expertise. With a unique process developed through extensive industry experience, G&P provides independent engineering, technical, inspection, and rectification services to OEMs and tiered suppliers across the manufacturing chain, alongside managing its own talent division.
G&P’s quality management consultants implement quality management systems, helping businesses experiencing challenges with their supply chain or facing quality or delivery issues to navigate the situation with confidence.
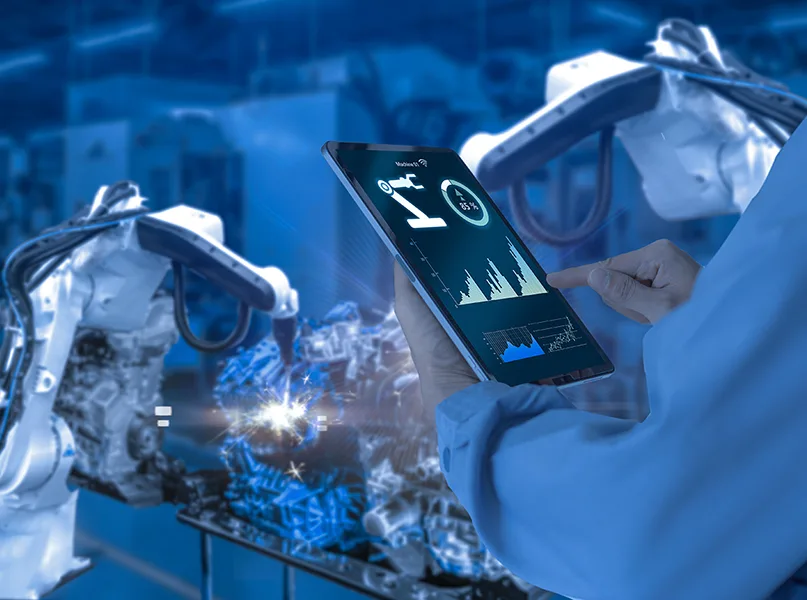
They can deploy agile and scalable resources skilled in supply chain quality management, including Advanced Product Quality Planning (APQP) to achieve Production Part Approval Process (PPAP) and Supplier Quality Assurance (SQA) to resolve issues and improve process capability.
The company has developed a service to deploy agile and scalable human resources, ranging from highly skilled vehicle technicians integrated directly in OEM operations, identifying and rectifying build issues, to programme managers and supplier quality engineers working in the supply chain to improve quality and capability at source.
Its highly skilled teams can inspect, identify, and rectify non-conformances, address root causes, use real-time data analysis to track and trace every element across the manufacturing supply chain, and even set up supply chain firewalls to prevent out-of-spec components from reaching the final production line.
By rectifying these upstream issues through quality inspection, containment, control, and rework, OEMs can prevent disruption within operations whilst ensuring manufacturing teams can deliver their original build schedule.
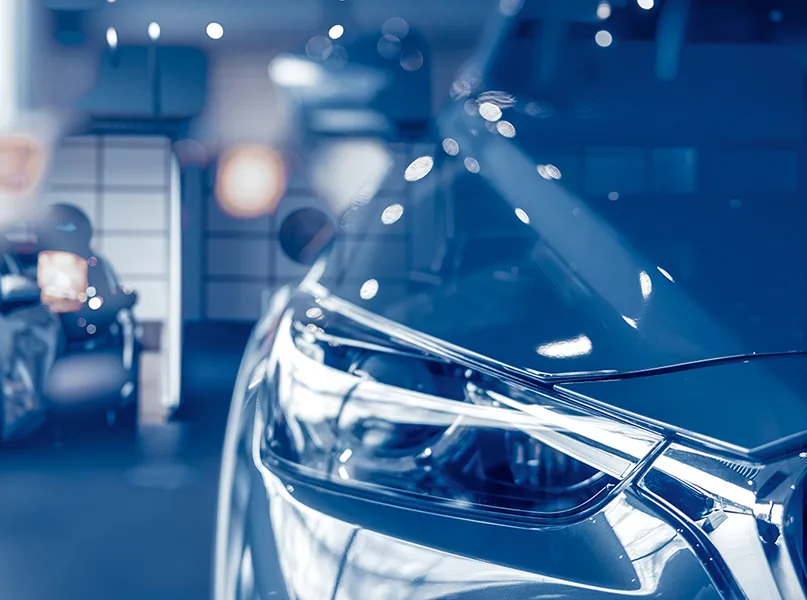
G&P has a proven track record of working with its customers to develop a deep understanding of their unique quality, efficiency, and profitability requirements to provide meaningful programme outcomes.
The company has developed the capability to implement these processes quickly for emergency situations or as part of a longer-term managed service to control the quality of components coming into manufacturing operations and prevent unnecessary disruption.
Working with an external quality management partner brings a number of benefits. First, it relieves pressure on in-house teams. Secondly, it is a well-tested route to quickly and efficiently identify quality issues and implement solutions in a timely and cost-effective manner.
Finally, it allows customers to leverage the knowledge and abilities of a highly skilled team with decades of accumulated experience across multiple manufacturing industries.